AMP Laboratory
Who We Are?
We are a multi-disciplinary group of engineers and scientists focused on solving metals material challenges.
Core Technology Areas:
- Cold Spray Technology
- Laser Additive Manufacturing
- Friction Stir Welding/Processing
- Plasma Surface Engineering (PVD, plasma electrolytic oxidation)
Our Mission
Research, Workforce Development and Education, Engineering Service, Outreach
To train and equip the next generation of materials and design engineers in advanced metals processing technologies, and to aid the industry and the nation in developing those technologies for real life applications that will bolster the American manufacturing enterprise.
Research Focus Areas
Materials joining Repair technology Additive manufacturing |
Energetic & ballistic material Structure-property-relationships Advanced/functional coatings |
Research
Gas Dynamics of Cold Spray & Control of Deposition (with Video Exhibits)
Ozan C. Ozdemir and Christian A. Widener
January, 2017
Reza Rokni
Ph.D. Dissertation Defense
April, 2015
Recent Journal Articles
- Rokni, M.R., Widener C., and Champagne V.R., “Microstructural Stability of Ultrafine Grained Cold Sprayed 6061 Aluminum Alloy,” Applied Surface Science 290 (2014) 482-489.
- Rokni, M. R., Widener, C. A., Ahrenkiel, S. P., Jasthi, B. K., & Champagne, V. R., “Annealing behaviour of 6061 aluminium deposited by high pressure cold spray. Surface Engineering,” 22 (2014) 63-69.
- Rokni, M. R., Widener, C. A., and Champagne, V. R., “Microstructural Evolution of 6061 Aluminum Gas-Atomized Powder and High-Pressure Cold-Sprayed Deposition,” Journal of Thermal Spray Technology, 2014, 1-11.
Recent Conference Proceedings
- Hammel, Joshua, Langerman, Michael, and Saunders, Nathan, “Radiometric and Metallurgical Analysis of Zone Formation in Elementary Laser Deposited Thin-Wall Structures,” IMECE2013-62142, ASME 2013 International Mechanical Engineering Congress & Exposition, November 15-21, 2013.
- Widener, C.A.; Franklin, J.; Jasthi, B.K.; West, M.K., “Mechanical Properties of Repaired 7075-T73 Friction Stir Butt Welds,” 2013 TMS Annual Meeting, Friction Stir Welding and Processing VIII, March 5-7, 2013.
- Timothy Johnson, Todd Curtis, Bharat Jasthi, Eric East, Christian Widener, Michael West, “Effect of Friction Stir Processing on Armor Grade Materials,” 2013 TMS Annual Meeting, Friction Stir Welding and Processing VIII, March 5-7, 2013.
- Bharat Jasthi, Erik Klinckman, Todd Curtis, Christian Widener, Michael West, Robert Ruokolainen, Ashish Dasgupta, “Effect of Post-weld Aging on the Corrosion Resistance and Mechanical Properties of Friction Stir Welded Aluminum Alloy 7475-T73,” 2013 TMS Annual Meeting, Friction Stir Welding and Processing VIII, March 5-7, 2013.
- Blosmo, D.J., T. Curtis, T. Johnson, N. Procive, C.A. Widener, B. Carlson, R. Szymanski, and M.K. West, FSSW of Mg to Al with a Cold Sprayed Interlayer, TMS Annual Meeting 2011: San Diego, CA. p. 409-416.
- Procive, N., D. Blosmo, T. Johnson, T. Curtis, M. West, and B. Jasthi, C. Widener, Friction Stir Processing of Cold Spray Depositions for Enhanced Surface Properties, in MS&T'11. 2011: CD-ROM, Columbus, OH.
- Widener, C.A.; Blosmo, D.J.; Curtis, T.; Jasthi, B.K., “Investigation of the Repair of Aluminum Cladding Using Supersonic Cold Spray for Corrosion Protection,” 2011 DOD Corrosion Conference, La Quinta, CA, July 31-August 5, 2011.
- Joshua J. Hammell, Christopher J. Ludvigson, Michael A. Langerman and James W. Sears, “Thermal Imaging of Laser Powder Deposition for Process Diagnostics,” ASME 2011 International Mechanical Engineering Congress and Exposition, November 11–17, 2011.
- Sylva, G. and Widener, C.A. “Development of Simultaneous Opposed Welding of Al-7249 Extrusions with Large Recrystallized Grains Using the Self Reacting FSW Process,” 8th International Friction Stir Welding Symposium, Strand, Germany, May 18-20, 2010.
Patents
Widener, C.A., Hrabe, R.; Champagne, V., “Cold Spray System With Upstream Mixing And Hand Held Spray Nozzle Suitable for Robotic Manipulation,” US Patent Application – 61/719,632, 2012. |
Widener, C.A.; Hrabe, R.; James, B.; Champagne, V.; Britton, O.; Well, A. ”System for Cold Spray Repair of Aluminum Aircraft Skin Fastener Holes,” US Patent Application - 61/719,641, 2012. |
Hrabe, R.; James, B.; Widener, C.A.; Champagne, V., “Cold Spray Wear Coating for Hydraulic Lines,” US Patent Application, 61/719,636, 2012. |
Articles Online
AMP Lab News
SD US Senator Press Release - 9/15/21
Grant Awarded to South Dakota School of Mines and Technology for DoD Cold Weather
Research
Forbes - 7/28/21
Cold Spray Technology Could Allow Air Force To Quickly Repair Aircraft Parts Instead Of Replacing
Them
Rapid City Journal - 2/23/14
Future being created at Rapid City business incubator
Argus Leader - 2/8/14
S.D. university scientists unite to reveal words behind the masks
Prairie Business - 10/25/13
ECONOMIC DEVELOPMENT:Public/private partnerships promote positive economic development
Ellsworth AFB News - 3/27/13
Cold spray could bring AF 10-1 investment return
Cold Spray News Links
Business Wire - 11/7/13
GE Researchers Experiment with 3D Painting to Build Up and Repair Parts
SERDP / ESTCP News – Fall 2013
Cold Spray Technology for Aircraft Component Repair
Fox News - 1/3/13
Can a cold, green, supersonic spray save the Black Hawk?
Capabilities
Core Technologies
Focused on advanced metals deposition technologies, we’ve strived to be nationally and internationally recognized for our contributions to these areas.
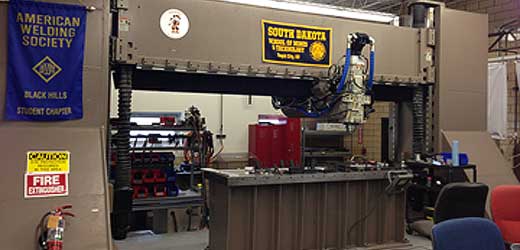
Friction Stir Welding
What is Friction Stir Welding
Friction stir welding is a completely solid-state welding process that relies on local forging and extrusion created by a rotating pin tool.
Advantages of Friction Stir Welding
-
No melting of materials
-
Low heat input into substrate –> Minimal degradation and/or distortion
-
Very high joint strengths possible -> Typically 70-90% joint efficiency
-
Full penetration joints in a single pass -> Thicknesses from 0.020 in. to 3 in.
-
Highly dissimilar materials can be joined
-
Virtually all metals and many plastics can be joined
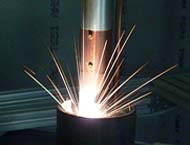
Laser Powder Deposition
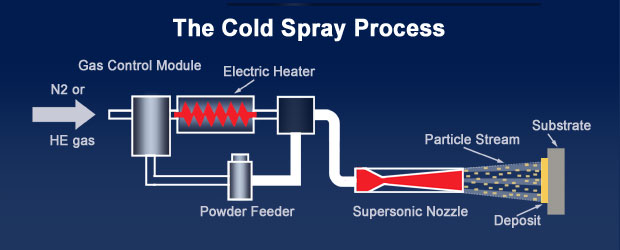
Cold Spray
Cold spray is a lower temperature solid-state thermal spray process that deposits metal powder using a heated inert gas through a supersonic nozzle.
Advantages of Cold Spray
- No melting of powder materials
- Low heat input into substrate –> Minimal degradation and/or distortion
- Very high adhesion strengths possible -> Greater than 10 ksi
- No limit on thickness -> Deposits can be from 0.001 in. to 1 in., or even more
- Highly dissimilar materials can be combined
- Virtually any metal can be deposited
- Deposition possible on both metallic and non-metallic surfaces
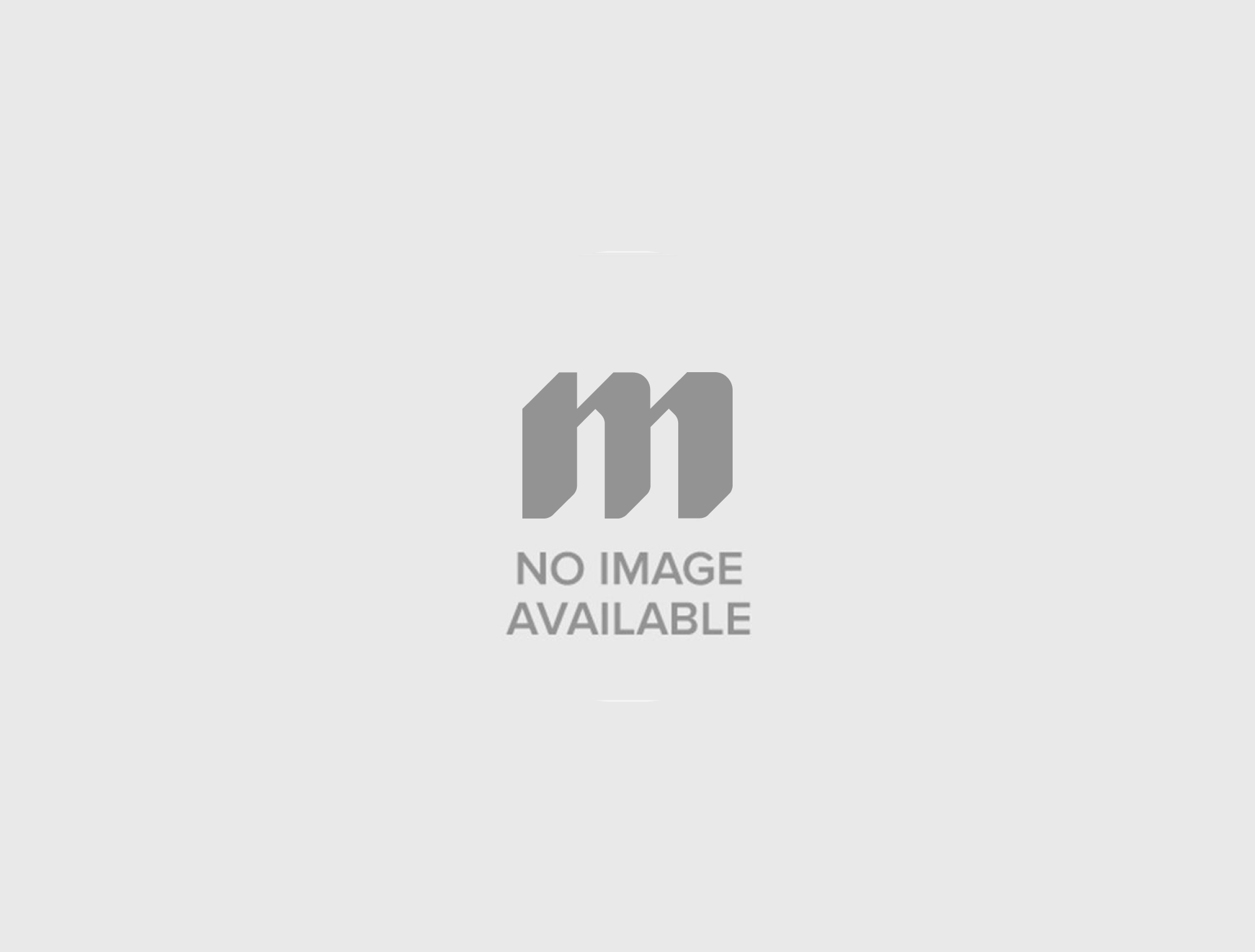
Plasma Surface Engineering
Plasma Vapor Deposition & Plasma Electrolytic Oxidation
Physical Vapor Deposition (PVD)
Solid target (metals, alloys, ceramics) vaporized by plasma, condensed on substrate (metals, ceramics, polymers, composites) to form thin films and coatings.
Applications: wear resistance, solid lubrication, optical & electronic layers
Plasma Electrolytic Oxidation (PEO)
High voltage electrochemical process where plasma discharges convert metal (Al, Ti, Mg, Zr) surfaces into hard, ceramic layers
Applications: wear resistance, corrosion resistance, thermal protection, biocompatibility.
Core Research Foci
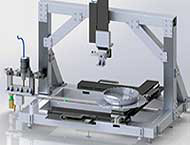
Advanced Manufacturing
Our newest capability brings 6-axis direct CAD-to-Motion path planning and tool changing capability for integrating multiple processes on a single platform.
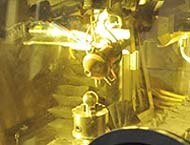
3-D Printing
Using both direct write and laser processing technologies, we are looking at how the future of manufacturing is changing by creating complex parts directly from computer models.
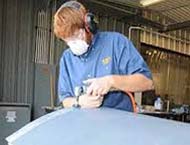
Repair
Helping industry and the Department of Defense find ways to save millions of dollars and the environment by repairing and remanufacturing parts instead of replacing them with new ones.
Other Capabilities
- Materials Characterization & Testing
- Prototyping
- Reverse Engineering
- Technology
AMP Lab Equipment
The lab is home to a range of state-of-the-art metals deposition and joining technologies, and is well instrumented for data capture of critical process parameters for both research and development and statistical process control evaluations for qualification.
Major Equipment
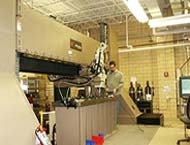
ISTIR 10 Friction Stir Welding 5-axis System
5-axis Motion with add'l forge and pin actuation for self-reacting and retractable pin tool welding. 7-axis force monitoring. Working envelope: 39” x 120” x 48” (X,Y,Z); Tool Rotation: 200-2000 rpm; Max. Forge Force: 20,000 lbs
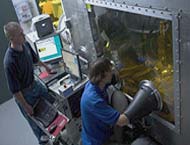
MTS/Optomec 3kW Laser Powder Deposition Sys.
This is a custom LENS based system using a TRUMPF 3kW Nd-YAG laser, and options for 3-6 axis, in or out of chamber, and 3-D printing or cladding, and internal bores to 2 in.
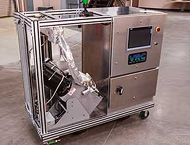
VRC Gen III Cold Spray High Pressure System
With the option for hand-held operation, and the capability to reach 1000 psi and 900 C, this system can do a lot.
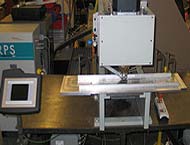
Riftec/HFW Refill Friction Stir Spot Welder
Refill Spot Welding system with 1-axis weld head. Produces flush, fatigue resistant friction stir spot welds. Material thicknesses up to 3/16” thick.

Kurt J. Lesker Company PRO Line PVD 200 Thin Film Deposition System
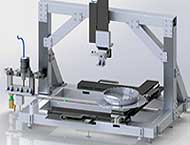
VDK 6000 Laser Deposition System
Advanced 6-axis motion system with CAD-to-Motion control using a Flexible Robotic Environment™ and a tool holder for both additive and subtractive, as well as inspection tools.
Lab Safety
The manuals, best practices and safety procedures available below are to be followed in order to insure safe practices in the AMP Laboratory.
South Dakota Mines Emergency Procedures Webpage
Other Equipment
|
Supporting Equipment
|
Other Equipment Available at South Dakota MinesExperimental Mining & Experiment Station
|
Have more questions?
Mailing address:
Attn: Grant A. Crawford – AMP
South Dakota School of Mines & Technology
501 E. Saint Joseph St.
Rapid City, SD 57701